تفاوت اصلی بین FMEA و DFMEA این است که FMEA برای محصولات، فرآیندها و خدمات در سازمان ها استفاده می شود در حالی که DFMEA فقط برای طراحی محصولات استفاده می شود.
دو نوع FMEA (تجزیه و تحلیل اثرات حالت شکست) وجود دارد: DFMEA و PFMEA. DFMEA مخفف Design Failure Mode Effects Analysis است در حالی که PFMEA مخفف Process Failure Mode Effects Analysis است. علاوه بر این، FMEA یک روش رایج است که می توانیم در بخش های تولید و مهندسی مشاهده کنیم. آنها خرابی احتمالی سیستم های خود و همچنین هزینه های عملیاتی و طراحی را کاهش می دهند.
FMEA چیست؟
FMEA مخفف Failure Mode Effects Analysis است. FMEA یک رویکرد گام به گام برای شناسایی تمام خرابی های احتمالی در یک طراحی، شکست در عملیات یا فرآیندهای مونتاژ، یا یک محصول یا خدمات است. روش FMEA همه خرابی ها را بر اساس احتمال و شدت شکست دسته بندی می کند. "حالت شکست" به هرگونه نقص یا خطا در طراحی، فرآیند یا مورد اشاره دارد که بر مشتری تأثیر می گذارد. در همین حال، تحلیل اثرات به بررسی پیامدهای شکست ها اشاره دارد.
علاوه بر این، FMEA دانش موجود و اقدامات مرتبط با خطرات خرابی را مستند می کند و از آنها برای بهبود مستمر استفاده می کند. FMEA معمولاً از اولین مراحل نظری طراحی شروع می شود و در طول عمر محصول یا خدمات ادامه می یابد.
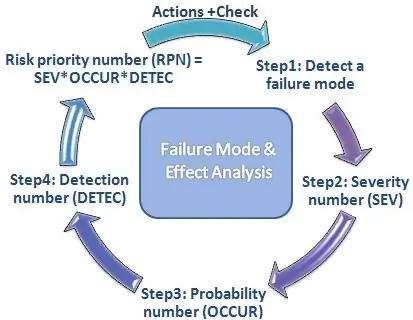
علاوه بر این، FMEA یک رویکرد پیشگیرانه است که علل بالقوه قبلی را شناسایی می کند تا خطاهای اصلی را بتوان بر این اساس اصلاح کرد تا از خطاهای عمده جلوگیری شود. این برنامه به طور گسترده در بخش تولید استفاده می شود.
FMEA در شرایط زیر استفاده می شود:
1. قبل از راهاندازی یک فرآیند، محصول یا خدمات جدید.
2. هنگام استفاده از فرآیند، محصول یا خدمات موجود به روشی جدید
3. قبل از توسعه برنامه های کنترلی برای یک فرآیند جدید یا تغییر یافته
4. به عنوان یک بهبود مستمر برای فرآیند موجود
5. هنگامی که شکایات یا شکست های تکراری در محصول، فرآیند یا خدمات موجود گزارش می شود
6. بررسی به موقع در طول عمر فرآیند، محصول یا خدمات
DFMEA چیست؟
DFMEA مخفف عبارت Design Failure Mode Effects Analysis است. این روش می تواند شکست های بالقوه در طراحی محصول را در مرحله توسعه شناسایی کند. در واقع، DFMEA برای اولین بار در علم موشک برای جلوگیری از شکست استفاده شد. امروزه بسیاری از صنایع از این روش برای شناسایی ریسک ها، اتخاذ اقدامات متقابل و جلوگیری از شکست استفاده می کنند. در بیشتر موارد، مهندسان از این به عنوان روشی برای بررسی احتمال شکست طراحی در یک موقعیت واقعی استفاده می کنند.
ابتدا، DFMEA تمام عملکردهای طراحی، حالت های خرابی و اثرات آنها را بر مصرف کننده با رتبه بندی شدت مربوطه شناسایی می کند. در مرحله بعد، علل اصلی و مکانیسمهای خرابی احتمالی آنها را شناسایی میکند. رتبه های بالا ممکن است منجر به اقداماتی برای جلوگیری یا به حداقل رساندن دلایل ایجاد حالت شکست شود. پس از انجام اقدامات توصیه شده برای خرابی های شناسایی شده، مرحله بعدی مقایسه مقادیر قبل و بعد از RPN است. RPN مخفف شماره اولویت ریسک است که ضرب شدت، وقوع و تشخیص است.
علاوه بر این، ابزار اصلی مورد استفاده برای DFMEA یک ماتریس DFMEA است. این ماتریس ساختاری را برای گردآوری و مستندسازی اطلاعات مرتبط از جمله مشخصات فنی، تاریخ صدور، تاریخ تجدیدنظر و اعضای تیم ارائه میکند. به طور کلی، DFMEA یک کار تیمی با تخصص فنی است و معمولاً شامل یک تیم متقابل است. علاوه بر این، DFMEA برای غلبه بر شکستهای احتمالی طراحی به کنترلهای فرآیند متکی نیست.
رابطه بین FMEA و DFMEA چیست؟
FMEA روش عمومی تجزیه و تحلیل اثرات حالت شکست است. DFMEA نوعی تجزیه و تحلیل اثرات حالت شکست (FMEA) است که برای طراحی محصولات در مرحله توسعه طراحی انجام می شود. هر دو شکست های احتمالی، شدت خطرات، کنترل های موجود، توصیه ها و بهبودها را پس از اقدامات توصیه شده ارزیابی می کنند.
علاوه بر این، هدف نهایی تجزیه و تحلیل اثرات حالت شکست، کاهش یا اجتناب از خطاهای عمده محصولات، فرآیندها یا خدمات است که در نهایت هزینه طراحی یا عملیات را کاهش می دهد.
تفاوت بین FMEA و DFMEA چیست؟
FMEA اصطلاح رایج برای تجزیه و تحلیل اثرات حالت شکست است در حالی که DFMEA نوعی FMEA است. علاوه بر این، تفاوت اصلی بین FMEA و DFMEA در کاربرد آنها است. روش FMEA برای محصولات، فرآیندها و خدمات در سازمان ها استفاده می شود در حالی که DFMEA فقط برای طراحی محصولات استفاده می شود.
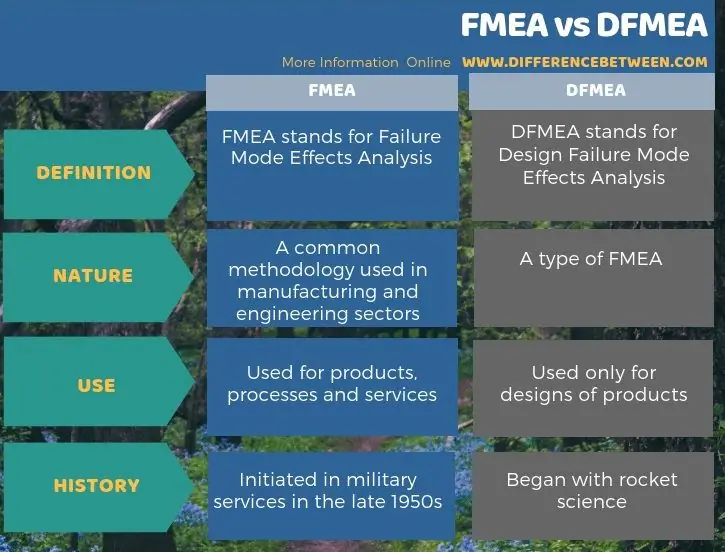
خلاصه - FMEA در مقابل DFMEA
تفاوت اصلی بین FMEA و DFMEA در این است که FMEA مخفف Failure Mode Effects Analysis است و اساس روش است در حالی که DFMEA مخفف Design Failure Mode Effects Analysis و نوعی FMEA است..