تفاوت اصلی بین PFMEA و DFMEA در این است که PFMEA به تجزیه و تحلیل شکستهای احتمالی یک فرآیند خاص از یک واحد تجاری کمک میکند در حالی که DFMEA به تجزیه و تحلیل شکستهای بالقوه طراحی یک محصول کمک میکند.
روش FMEA (تجزیه و تحلیل اثرات حالت شکست) به شناسایی حالت های بالقوه شکست یک فرآیند در مدیریت عملیات و طراحی در مرحله توسعه محصول در یک سیستم کمک می کند و خرابی ها را بر اساس احتمال و شدت شکست طبقه بندی می کند. حالت شکست به هرگونه نقص یا خطا در یک طراحی، فرآیند یا یک آیتم اشاره دارد که بر مشتری تأثیر می گذارد. "تحلیل اثرات" به مطالعه پیامدهای شکست ها اشاره دارد.
PFMEA چیست؟
PFMEA مخفف عبارت Process Failure Mode Effects Analysis است. این روش میتواند حالتهای شکست احتمالی را در فرآیندها در سطح عملیات شناسایی کند. به طور کلی، یک تیم با تجربه فنی PFMEA را انجام می دهد. فرآیند اساسی جمع آوری داده های کافی برای علل حالت های خرابی برای اصلاح یا به حداقل رساندن اثرات حالت شکست است.
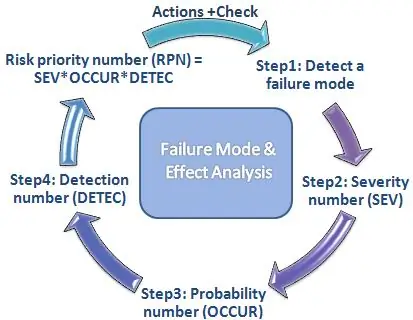
علاوه بر این، PFMEA یک ابزار ساختار یافته است که توسط انواع سازمان ها استفاده می شود. به ایجاد اثرات حالت های شکست کمک می کند و اقدامات لازم برای کاهش خطر را اولویت بندی می کند. PFMEA قبل از راه اندازی هر فرآیند جدید برای کاهش خطرات احتمالی مستند و ارائه می شود. علاوه بر این، به منظور دستیابی به بهبود مستمر سیستم، این امکان برای فرآیندهای غالب نیز وجود دارد.
DFMEA چیست؟
DFMEA مخفف عبارت Design Failure Mode Effects Analysis است. این روش به شناسایی شکست های بالقوه در طراحی محصول در مرحله توسعه کمک می کند. در بیشتر موارد، مهندسان از این به عنوان روشی برای بررسی احتمال شکست طراحی در یک موقعیت واقعی یا استفاده استفاده میکنند.
مهندسین ابزار اولیه برای DFMEA یک ماتریس DFMEA است. این ماتریس ساختاری را برای گردآوری و مستندسازی اطلاعات مرتبط از جمله مشخصات فنی، تاریخ صدور، تاریخ تجدید نظر و اعضای تیم ارائه میکند. به طور کلی، DFMEA یک کار تیمی با تخصص فنی و احتمالاً یک تیم متقابل است. علاوه بر این، DFMEA برای غلبه بر شکستهای احتمالی طراحی به کنترلهای فرآیند متکی نیست
شباهتهای بین PFMEA و DFMEA چیست؟
- PFMEA و DFMEA دو نوع تحلیل اثرات حالت شکست هستند.
- مراحل اساسی در DFMEA و PFMEA مشابه هستند، اما دو کاربرد متفاوت دارند.
- هر دو DFMEA و PFMEA نشان دهنده خرابی های احتمالی، شدت خطرات، کنترل های موجود، توصیه ها و بهبودها پس از اقدامات توصیه شده است.
- هدف نهایی هر دو کاهش یا اجتناب از خطاهای عمده محصولات و تولید است.
- این روششناسی ممکن است هزینه طراحی یا عملیات را نیز کاهش دهد.
- علاوه بر این، ممکن است برخی از خرابیها در DFMEA کاهش نیابد. این خرابیها را میتوان به PFMEA برای انجام کنترلهای لازم برای بهبود محصول منتقل کرد.
تفاوت بین PFMEA و DFMEA چیست؟
تفاوت اصلی بین PFMEA و DFMEA این است که PFMEA شامل فرآیندها می شود در حالی که DFMEA شامل طراحی محصول است. هدف اولیه DFMEA کشف اشکالات بالقوه طرح های محصول است در حالی که هدف اولیه PFMEA کشف شکست های بالقوه فرآیندها است. بررسی اولیه DFMEA با استفاده از شماتیک محصول انجام می شود، در حالی که PFMEA با استفاده از نمودار جریان فرآیند انجام می شود.تفاوت دیگر بین PFMEA و DFMEA این است که PFMEA در سطح عملیاتی اتفاق می افتد در حالی که DFMEA در مرحله توسعه اتفاق می افتد.
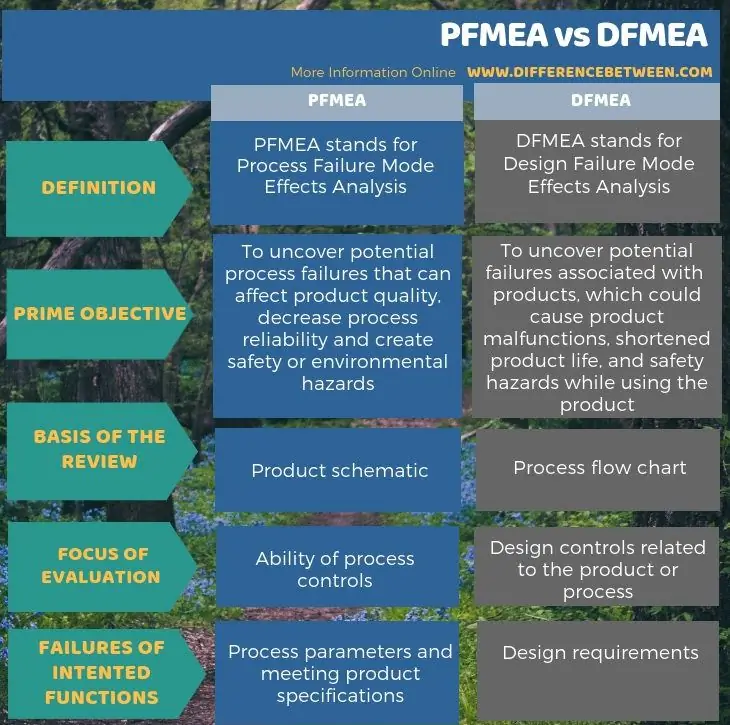
خلاصه- PFMEA در مقابل DFMEA
تفاوت اصلی بین PFMEA و DFMEA در این است که PFMEA به تجزیه و تحلیل خرابیهای بالقوه یک فرآیند خاص در سطح عملیات کمک میکند در حالی که DFMEA به تجزیه و تحلیل شکستهای بالقوه طراحی محصول در سطح طراحی و توسعه کمک میکند. علاوه بر این، این روشها هزینههای تولید و همچنین شکستهای احتمالی در عرضه محصول را کاهش خواهند داد.