FMEA در مقابل FMECA
هر دو، FMEA و FMECA، دو روش مورد استفاده در فرآیند تولید هستند و واقعیت اساسی در تفاوت بین FMEA و FMECA این است که یکی پسوند دیگری است. برای توضیح بیشتر، تجزیه و تحلیل حالت و اثرات شکست (FMEA) و حالتهای شکست، تجزیه و تحلیل اثرات و بحرانی (FMECA) دو نوع تکنیکی هستند که در شناسایی خرابیها یا خطاهای خاص در یک محصول یا فرآیند و انجام اقدامات اصلاحی به منظور تصحیح مشکلات استفاده میشوند. چالش ها و مسائل؛ و FMECA توسعه ای برای FMEA است. این مقاله تجزیه و تحلیل بیشتری از تفاوت بین FMEA و FMECA را به شما ارائه می دهد.
FMEA چیست؟
FMEA مخفف Failure Modes and Effects Analysis است و می توان آن را به عنوان یک رویکرد گام به گام برای تعیین خرابی ها یا خطاهایی که در فرآیندهای ساخت، طراحی یا مونتاژ یا در محصولات یا خدمات رخ می دهد در نظر گرفت.
حالتهای شکست به معنی حالتها یا روشهایی هستند که بر خرابیها تأثیر میگذارند. شکست ممکن است منجر به نارضایتی مشتری شود که ممکن است منجر به کاهش حجم فروش شود. تحلیل اثرات به مطالعه پیامدها یا دلایل آن شکست ها اشاره دارد. بنابراین، هدف FMEA برداشتن اقدامات/گامهای لازم برای حذف یا کاهش خرابیها است که با اولویتترین آنها شروع میشود.
FMEA در مرحله طراحی به منظور جلوگیری از خرابی استفاده می شود. سپس در مرحله کنترل، قبل و در حین عملیات جاری فرآیند استفاده می شود. FMEA باید در اولین مراحل مفهومی طراحی شروع شود و باید در طول عمر محصول یا خدمات ادامه یابد.
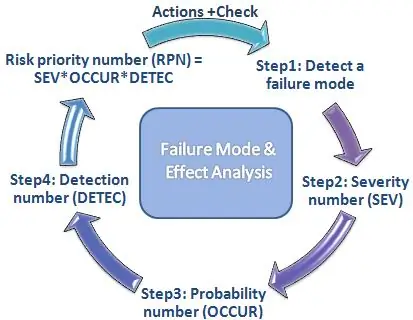
FMEA را می توان دراستفاده کرد
• طراحی یا طراحی مجدد فرآیند، محصول یا خدمات پس از استقرار عملکرد کیفیت.
• هنگام توسعه محصولی با ویژگی های بیشتر.
• قبل از تدوین برنامه های کنترلی برای یک فرآیند جدید.
• در زمان بهبود اهداف برای یک فرآیند، محصول یا خدمات موجود برنامه ریزی می شود.
• تجزیه و تحلیل شکست های یک فرآیند، محصول یا خدمات موجود.
FMECA چیست؟
FMECA نسخه بهبود یافته FMEA با افزودن بخش تجزیه و تحلیل بحرانی است که برای ترسیم احتمال حالت های خرابی در برابر تأثیر پیامدها استفاده می شود. FMECA را می توان به عنوان روشی برای شناسایی خرابی های سیستم، دلایل شکست و تأثیر آن خرابی ها نشان داد.با عبارت Criticality، فرآیند FMECA می تواند در شناسایی و تمرکز بر حوزه های طراحی با نگرانی بسیار مورد استفاده قرار گیرد.
بعلاوه، FMECA می تواند در بهبود طراحی محصولات و فرآیندها مفید باشد که منجر به قابلیت اطمینان بالاتر، افزایش ایمنی، کیفیت بهتر، کاهش هزینه و افزایش رضایت مشتری می شود. هنگام ایجاد و بهینه سازی برنامه های نگهداری برای سیستم های قابل تعمیر و سایر روش های تضمین کیفیت، این ابزار مفید خواهد بود.
علاوه بر این، هر دو FMEA و FMECA ملزم به رعایت الزامات کیفیت و ایمنی هستند، مانند ISO 9001، شش سیگما، شیوههای تولید خوب (GMPs)، قانون مدیریت ایمنی فرآیند، و غیره.
تفاوت FMEA و FMECA چیست؟
• روش FMEA فقط اطلاعات کیفی ارائه می دهد در حالی که FMECA اطلاعات کیفی و همچنین کمی را ارائه می دهد، که توانایی اندازه گیری را می دهد زیرا سطح بحرانی را به حالت های خرابی متصل می کند.
• FMECA توسعه FMEA است. بنابراین، برای انجام FMECA، باید FMEA و سپس تجزیه و تحلیل بحرانی انجام شود.
• FMEA حالت های خرابی یک محصول یا فرآیند و اثرات آنها را تعیین می کند، در حالی که تجزیه و تحلیل بحرانی آن حالت های شکست را به ترتیب اهمیت با در نظر گرفتن میزان شکست رتبه بندی می کند.